1. Material preparation: The mold materials required for different products are also different, and appropriate mold materials should be selected according to the characteristics of the product;
2. Rough processing: After selecting the data, use a milling machine or planer to stop the preliminary processing of the three-dimensional and front surface of the mold data.
3. Fine processing: It is required to use a grinder to process three-dimensional and four-corner squares. Grind the male splint, stripper plate, lower template and backing plate into three-dimensional shape and then make a right angle, and then grind the bottom plate and upper cover plate into three-dimensional shape.
4. Scribing: Place the mold plate that has been ground and smashed at a right angle after fine processing on the scribing table. According to the mold manufacturing drawing, use the scribing height ruler to stop the scribing, and initially stop the scribing mold plate Rush, drill, tap.
5. Heat treatment: After low temperature quenching, tempering, quenching and tempering, and annealing of the plates that require heat treatment of the lower template and modules to increase the hardness, the plate is stopped for three-dimensional grinding and right-angled, and then the wire cutting process is stopped.
6. Assemble the test mold: select the mold base or the supporting guide post and the guide sleeve to complete the mold assembly, and stop the debugging and punching of the assembled mold device on the punching machine, and initially measure the punch out to confirm whether it fits the product. Requirements, complete the entire stamping process.
Production process of stamping parts factory
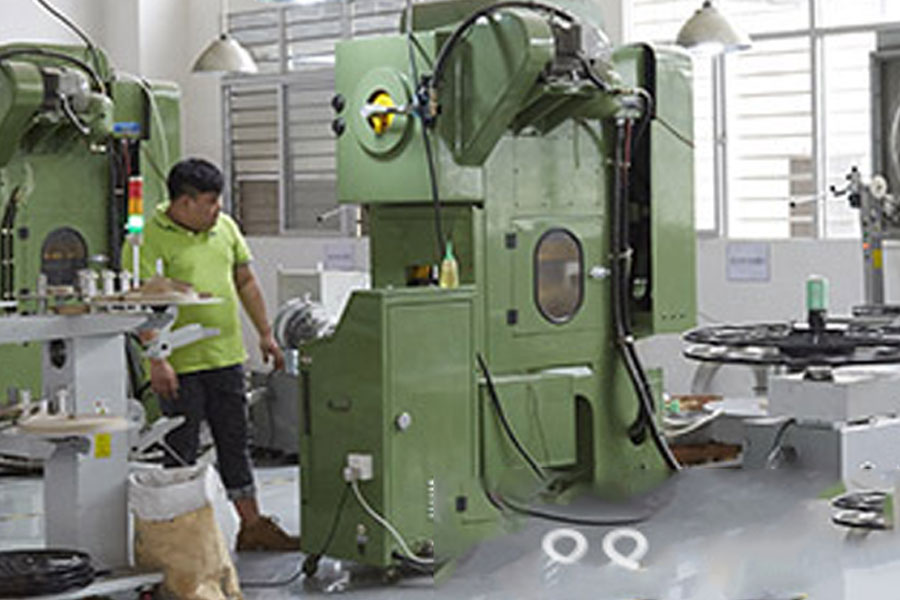
Leave a Reply