There is a process in the stamping process called stretch forming, this process is one of the main processes of stamping process, all Metal Stamping processes will use this stretch…
Introduction to the stretch forming process of metal stamping
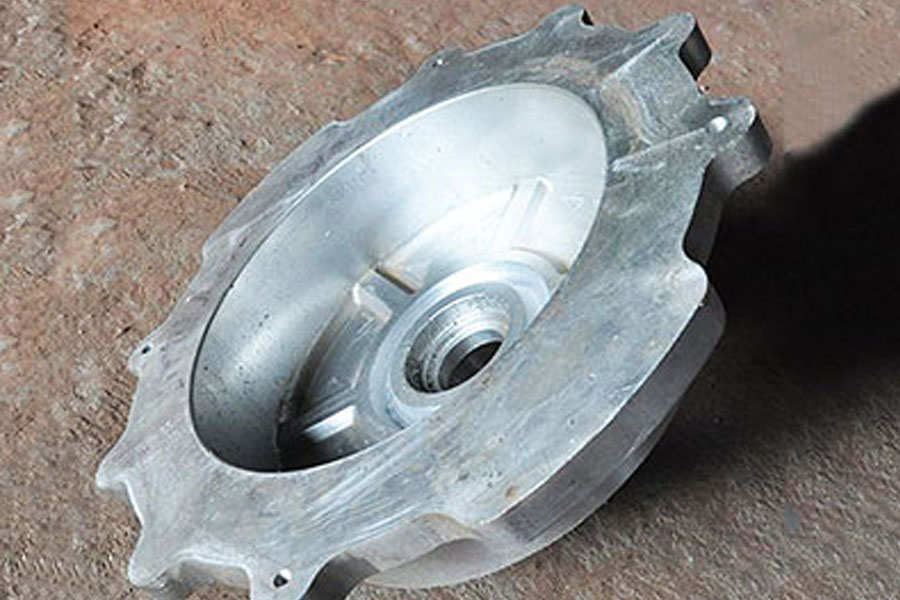
There is a process in the stamping process called stretch forming, this process is one of the main processes of stamping process, all Metal Stamping processes will use this stretch…
1. During the use of Metal Stamping dies, punch breakage, twists, and gnawing will occur. Punch sleeves are usually gnawed, and the damage of punches and sleeves is generally replaced…
1. There is no need for excessive consumption of materials; after stamping, the weight of stamped parts is greatly reduced and the hardness is well maintained. After plastic deformation, the…
1. Before stamping, there must be plate straightening adjustment process steps or automatic correction tooling to ensure that the raw materials enter the mold cavity smoothly. 2. The position of…
1. Improve the rationalization level of the process. 2. Improve the mold design level, reduce the process, and increase the life of the mold. 3. Improve the automation and high-speed…
1. Metal Stamping parts should be strictly inspected before installation and use, dirt should be removed, and the guide sleeve and die of drawing stamping parts should be carefully checked…
1. The protection of the stamping die working area by the stamping parts processing plant 1. Install protective devices around the stamping die. 2. Reasonable design of molds reduces the…
7GA = 4.5mm 10GA = 3.2mm 11GA = 3.0mm 13GA = 2.3mm 14GA = 2.0mm 16GA = 1.6mm 17GA = 1.4mm 18GA = 1.2mm 20GA = 1.0mm
Passive: Passive electronic components are one of the most commonly used parts in the entire industry. These components do not transfer energy like their active components, and can only use…
1. The mold core positioning hole is worn out due to frequent and multiple combinations of the mold core, resulting in large gaps after assembly (looseness after assembly) or uneven…